Togouchi Hikimono, Kurimono[Traditional Crafts designated by Hiroshima Prefecture]Kobo Shintaku / Akino Kijakushi LLC, Yokohata Kogei
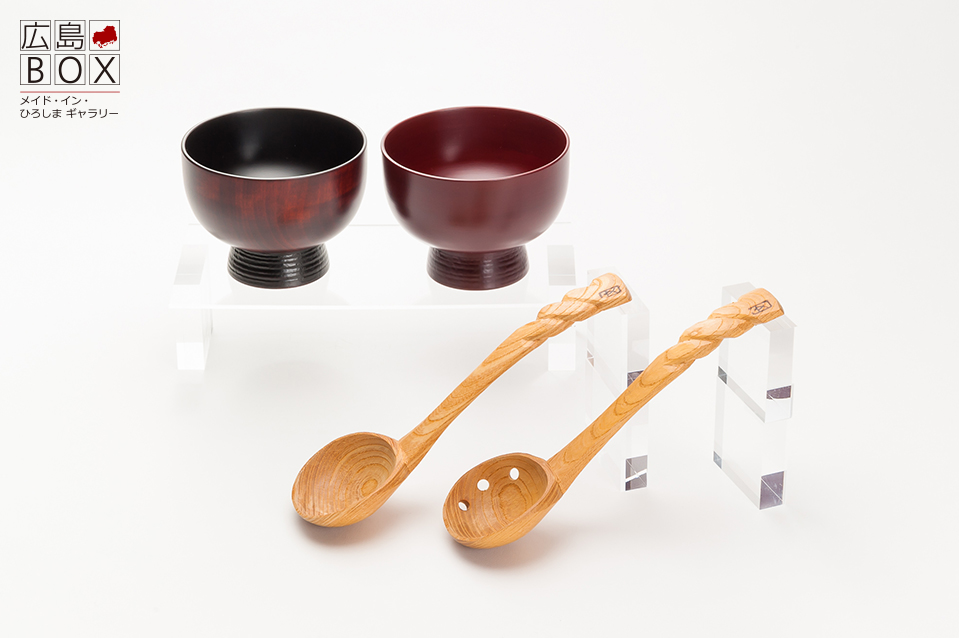
Exhibitor (Manufacturer) | Kobo Shintaku / Akino Kijakushi LLC, Yokohata Kogei |
---|---|
Address | 306-4 Togouchi, Aki-Ota-cho, Yamagata-gun, Hiroshima / 335 Yoshiwago, Aki-Ota-cho, Yamagata-gun, Hiroshima |
TEL | (0826)28-2109 / (0826)28-2063 |
Representative | Shintaku Tomoya |
Job description | (Kobo Shintaku) We manufacture lacquerware using only pure, domestic laquer and domestic wood, naturally dried and worked on a lathe. (Akino Kijakushi LLC, Yokohata Kogei) Manufacture of Togouchi Kurimono |
Togouchi Hikimono (Togouchi Grind Ware)
The origins of this product are said to be from 1900 when Ishida Tomiji moved to Togouchi-cho (current Aki-Ota-cho, Yamagata-gun) from Shimane Prefecture and conveyed the techniques of “wooden base manufacturing (Kiji-shi) “and “lacquer painting (Nu-shi).” “Togouchi Hikimono” in which wood is cut out rotated by a potter’s wheel, can be finished by lacquer. Since the beauty of wood grains is determined by the edge of a cutter, it is one of the features that a craftsman manufactures cutters fit for the wood base for himself and it is said ‘”a person cannot be a “Kiji-shi” unless he can perform “forging”’
Originally, “Kiji-shi” and “Nu-shi” were separately manufacturing lacquer wares, but now only one person conducts all the processes from lumber to painting. Now, only one manufacturing company remains, it preserves traditional techniques and actively takes on the manufacturing of new products.
●Wood base manufacturing
(1) Rough cutting (2) Natural drying (3) ”Nakaguri (boring)” cut removing distortions (4) Finish
*Repeat “drying” and “boring” until distortions are corrected.
Natural drying over one year
●Lacquer painting
White wood products finished with a wooden base can be finished as a “lacquer ware.” In lacquer painting, we only use Japanese lacquer with layers of paint much thinner lacquer techniques from abroad.
Lacquer painting by Japanese lacquer
Togouchi Kurimono (Scoop)
It is said that it was created by Fujiya Daisuke, a craftsman from Miyajima-zaiku in the late Edo Era. In the Taisho Era, Fukuda Rikichi settled in Togouchi-cho (now Aki-Ota-cho, Yamagata-gun), the source of the materials from Miyajima and conveyed the techniques.
“Togouchi Kurinomo” does not use a “grinder/sand paper” in any process and finishes only by cutters. It manufactures exclusive tools according to the shape to be made, including such small articles as teaspoons and sauce ladles with a deep scoop. It is one of the features of “Togouchi Kurinomo” that the variety of tools is extensive.
“Exclusive tools are hung on the wall (left in the photo)” and “yari-gannna (plane) (right in the photo) the top of which is bent is used for scooping.
Fujo Otama (Floating Ladle)
It is regarded as a lucky article as it floats from the bottom when being used for serving soup and called “Fujo Otama.” “Fujo Otama” is comprised of 16 processes in total, including “wariki mokko (wood cutting woodwork), cutting wood by a chopper like wood-chopping, and manufactured with 12 kinds of tools.
■9th process “Inside Finish”
Production of a hollow of otama by “yari-gannna.” As no grinder is used, it is finished it is carefully finished so that no scuffing ever appears.